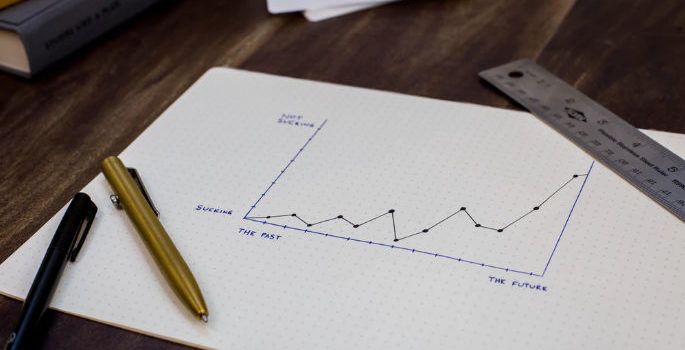
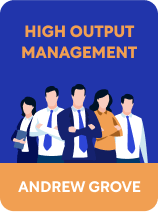
This article is an excerpt from the Shortform book guide to "High Output Management" by Andrew S. Grove. Shortform has the world's best summaries and analyses of books you should be reading.
Like this article? Sign up for a free trial here .
What are the steps in the production process? How do they work?
There are three important steps in the production process. You’ll need to learn to increase output in all steps of production.
Read more about the steps in the production process and why they’re important.
Three Steps in the Production Process
There are three steps in the production process in a factory. Thinking about these steps can help you both maximize production output, and think of other business workings as factory productions.
Step #1: Process and Step #2: Assembly
The first two steps in the production process go together. To determine the fastest, most cost-effective way to produce products in a factory, manufacturers first determine throughput times (how long it takes to prepare individual product parts) and then offset them (start them at staggered times so they’ll all be completed at the same time and ready for assembly). To do this:
1. Determine the limiting stage, which is making the component that’s most time-consuming, valuable, or sensitive. You’ll organize your workflow around this stage.
- Manufacturing example: If you’re working as a cook at a restaurant that makes breakfast consisting of toast, boiled eggs, and coffee, the limiting step is boiling the egg, which takes the longest at three minutes.
- Business example: In the Intel workflow for hiring new graduates, the limiting step is inviting them to visit an Intel plant because it’s the most expensive step—Intel pays for the students’ travel and managers spend a lot of paid time showing the students around.
2. Determine how long the next-longest stage will take. You’ll time starting this stage so the component is ready at the same time as the limiting stage.
- Manufacturing example: This is toasting the bread, at one minute. You’ll start toasting the bread two minutes before the egg will be ready.
- Business example: Another step involved in hiring a new graduate is on-campus interviews, which needs to be done far enough in advance to make travel arrangements for the students who are then invited to tour the plant.
3. Repeat step #2 for all stages.
- Manufacturing example: The final stage in the breakfast example is pouring the coffee, which takes only seconds. You’ll start this stage seconds before the toast will be ready.
- Business example: An earlier step in hiring new graduates is to do phone screenings to determine who should be interviewed. This needs to be done early enough to make travel arrangements for on-campus interviews.
4. Calculate the assembly time and add the assembly time to the time required for the limiting stage to get the total throughput time.
- Manufacturing example: This is how long it will take you to get the toast out of the toaster, the egg out of the pot, the coffee out of the maker, and arrange all these components on a tray.
- (Shortform business example: The total throughput time for hiring a new graduate is the time between preparing a job posting and a students’ graduation, after which they start work.)
Complications
Three things might complicate these steps in the production process:
1. Limited equipment availability. If you don’t have constant access to equipment, you need to factor waiting time into your throughput time. Waiting time could make a different component’s production the limiting step.
- Manufacturing example: If there are multiple cooks making breakfast at the same time, you may have to wait for the toaster. If you have to wait five minutes for the toaster, you’ll have to get the toast started (find the bread) before you boil the egg.
- (Shortform business example: If you run a photo printing shop, all of your employees will need to use the photo printer at some point. If it takes ten minutes to print photos and the line for the printer is always three employees long, that adds half an hour to the printing step.)
2. Offsetting conflicts. If you’re in the middle of one task at the moment you’re supposed to start another, you’ll throw off the timing because you can’t do both things at once. You could ask someone else to help you, but this isn’t dependable. There are three better ways to handle this:
Option #1: Specialization. Assign everyone involved in the process to a single task, and then combine everyone’s work at the end to create multiple final products (instead of everyone individually making their own product). The downside is that specialization is expensive because you need more staff.
- Manufacturing example: Imagine you’ve been promoted from server to manager at the breakfast cafe. Hire one person to make the toast, one to cook the egg, one to pour the coffee, and one to organize everyone.
- (Shortform business example: In the photo printing shop, you might hire just one employee to operate the photo printer, one employee to package the printed photos, and one employee to operate the cash register and deal with customers.)
Option #2: Purchase more capital equipment. Buy more of whatever tools are needed to complete the limiting step. The downside is the expense of doing this.
- Manufacturing example: If the limiting step is making the toast because you don’t have enough toasters to toast all of the required bread, buy another toaster.
- (Shortform business example: In the photo printing shop, you may buy another printer.)
Option #3: Increase inventory. Make as many products as you can, so that you’ll have constant access to products so you can supply them as soon as orders come in. The downside is that you’ll have to throw away the extra, which can be expensive.
- Manufacturing example: If the kitchen constantly churns out breakfasts, there will always be one available when a customer arrives, but you’ll have to throw out a lot of food as it cools and spoils and is no longer servable.
- (Shortform business example: If you run a toy shop that sells Christmas-themed decorations, order extra wreaths and reorder every time someone buys something. You’ll never run out of stock, but you will have wreaths left over after Christmas when no one will want to buy them, and you’ll have to throw them out.)
Choose the most cost-effective option. Do this by studying the pluses and minuses of each factor. You don’t have to use math or a stopwatch; you just need to reflect enough to understand the relationships between everything involved in your production process.
- Manufacturing example: The ideal breakfast solution is to buy a continuous egg-boiler and toaster and assign each piece of equipment a specialized operator. In addition to expense, another downside is lost flexibility—customers can’t get a longer-cooked egg—but the advantages are lower cost and more consistent food quality.
3. Unexpected events. Unforeseen circumstances (such as equipment breakdown) can cause delays and upset the production process. To avoid this, build “slack” (extra time or resources) into the system so that if there’s a delay, you can make up for it.
The easiest way to create slack is to build extra inventory. The best way to balance the cost of building this extra inventory is to keep the inventory at the earliest possible production stage: For instance, keep extra raw materials rather than extra completed products. In every production flow, the material gains value at each step of the process. For example, toast is more valuable than bread, and a three-piece breakfast is more valuable than an egg, toast, and coffee separately. Keeping the inventory at the lowest-value stage saves you money, as if you do have to dispose of the extra inventory for any reason, you’re losing cheap raw materials rather than expensive finished products.
- Manufacturing example: Store extra raw (not boiled) eggs. Raw eggs are cheaper than boiled ones and won’t spoil as quickly.
- (Shortform business example: In the toy shop, store extra crafting materials used to make the Christmas wreaths, not extra wreaths. You may be able to reuse the materials for other non-seasonal products.)
Step #3: Testing
The last of the steps in the production process is testing. Testing examines the raw materials, parts, or the final product for flaws. First, we’ll look at when you should test, and then we’ll look at the different ways you can carry it out.
Timing of Tests
As we learned, material gains value as it passes through each production stage. Therefore, you should always try to catch problems at the lowest possible stage to save yourself money.
You should test at three different points during production:
Point #1: Upon Receipt of the Raw Materials
This is also called an incoming or receiving inspection. If you can catch any problems at this early stage, you can avoid contaminating the whole product with one bad component.
- Manufacturing example: If your eggs are rotten, you’ll have to throw out all the breakfasts you make with them, wasting toast and coffee as well. If you can reject the eggs before you even get started, you’ll save other raw materials.
- (Shortform example: If one of your tasks is to organize the printing of a festival program, look at the page proofs as early as possible so that if there’s a critical mistake, you can fix it before printing samples or the final program.)
If raw material inventory doesn’t meet your standards, you have two choices:
Choice #1: Send it back. If you do this, you won’t be able to build anything until you replenish your supply, which may cost you in lost opportunity.
To avoid getting into this situation, purchase extra raw material inventory. The general rule is that you should have enough to last you the amount of time it would take to replace your inventory.
- Manufacturing example: If you get eggs delivered once a day, you should always keep a day’s worth of eggs, so that if one day, the entire delivery is rotten, you have enough to last until the next delivery. The rule is general because having inventory costs money (storage space costs money), so you have to consider the trade-off.
- Business example: In a managerial sense, raw inventory is yet-to-be-started discretionary projects that aren’t urgent. You should have these backburner tasks to work on so that when you get free time, you aren’t tempted to micromanage or interfere with your subordinates’ work.
Choice #2: Use it anyway. If you do this, the quality of some of your final products will be lower.
In manufacturing, the decision is usually based on cost—which is more expensive, an idle factory, or a lower-quality product? (To decide, manufacturers gather managers from the manufacturing, design engineering, and quality assurance departments to discuss.)
However, there is one hard rule: Never use unacceptable material if it could cause your product to completely fail, which is called a reliability problem. Complete failure has unpredictable and potentially dangerous consequences.
- (Shortform manufacturing example: If your company makes bicycle helmets and the paint you use to color them blue is the wrong shade, go ahead and use it. If there’s something wrong with the life-saving parts of the helmet, don’t use them, because someone could die.)
Point #2: In Process
These tests check the components while they’re at various stages of completion. There are two types:
Type #1: Functional, which involves destroying a product to check its quality.
- Manufacturing example: You might occasionally open an egg after it’s been boiled to make sure it’s cooked properly.
Type #2: Process, which involves checking the process that makes the product. This option is generally better because you don’t have to destroy any product.
- Manufacturing example: You might check the temperature of the egg-cooking water using a thermometer to make sure it’s hot enough to boil the eggs.
Point #3: After Assembly
This is also called the final or outgoing quality inspection. The final, assembled product is tested.
- Manufacturing example: You might look at the plate of breakfast to make sure all the components are there. You can visually confirm that they’re hot and cooked by looking for steam.
- (Shortform business example: You might look at a report by a subordinate when it’s fully completed and about to be sent off.)
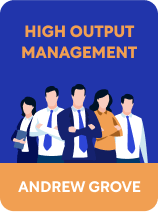
———End of Preview———
Like what you just read? Read the rest of the world's best book summary and analysis of Andrew S. Grove's "High Output Management" at Shortform .
Here's what you'll find in our full High Output Management summary :
- How to increase your managerial output and productivity
- The 11 activities that offer a higher impact on output
- How meetings can be used as a time management tool