
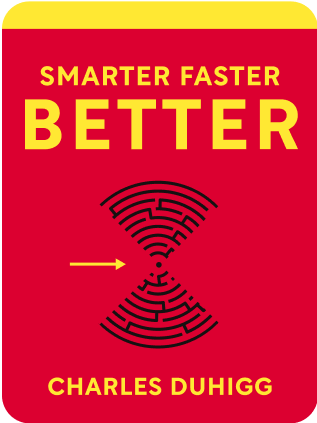
This article is an excerpt from the Shortform book guide to "Smarter Faster Better" by Charles Duhigg. Shortform has the world's best summaries and analyses of books you should be reading.
Like this article? Sign up for a free trial here .
What is a commitment culture, and what difference can it make in your organization? How can you build one and foster its growth?
In Smarter Faster Better, Charles Duhigg includes a culture of commitment on his list of ingredients for productivity. He explains what it is and discusses its benefits. Duhigg also outlines steps you can take to build a commitment culture and provides a real-world example so you can see it in action.
Read on to learn more about commitment culture.
What Is a Commitment Culture?
As its name would suggest, a commitment culture is a workplace culture in which the employer is committed to each employee; specifically, committed to each employee’s growth and success. It’s a culture in which employees are truly valued. Both managers and employees understand that everyone plays a vital role in the company’s success. Workers are given the room to make mistakes, learn from them, and improve their workflow accordingly. Employers are willing to invest in each employee’s growth even if that growth is slow.
When a commitment of this kind is shown to employees, they respond in kind and remain committed to the company. They’re driven to work harder because they genuinely care about the fate of the company and the work they’re doing. Workers will often choose to stay at the company even if they receive a better offer elsewhere. During hard times, such as recessions, the company and its employees are more likely to stick together: they want to weather the storm together.
In a commitment culture, a sense of trust develops between workers and employers. Employers trust their employees to do a good job and to help the company move forward. Likewise, employees trust their employers to have their backs, invest in their growth, and be tolerant of their mistakes (within reason).
This atmosphere of trust makes it easier for lean manufacturing to flourish. Workers are more likely to use the control they’ve been given, as they’re less worried about repercussions if their decisions don’t go to plan.
What Are the Benefits of a Commitment Culture?
In general, commitment cultures have proved to be hugely beneficial to companies. A study of Silicon Valley technology start-ups found that companies with a culture of commitment vastly outperformed their peers in many ways:
- None of the companies with this type of culture failed within the ten-year period of the study.
- Their profitability ratios were higher than those of companies with other types of culture.
- These companies went public faster than their competitors.
- Within these companies, employees abandoned personal agendas and rivalries with colleagues in favor of remaining committed to the company and its aims.
Companies with a culture of commitment also reap the benefits of having committed employees. Employee retention in such companies is often high, meaning companies don’t lose their workers’ expertise to a competitor. They also avoid having to spend time and money replacing their lost employees.
How Can You Create a Commitment Culture?
You can create a commitment culture using various methods. Firstly, implementing lean manufacturing can lay the groundwork for a commitment culture to flourish. Empowering people to make decisions is a way to show that you value them, are committed to their growth and success, and see them as important to the business. Having a small amount of control makes each worker feel like they can have an impact on the company’s success, which increases their commitment.
Likewise, lean manufacturing promotes the trust that’s key in a commitment culture. Every worker knows that they are trusted to do well. That’s why they were given power in the first place.
Outside of the principles of lean manufacturing, there are some other actions you can take to create a culture of commitment. For example, the companies in the Silicon Valley study that successfully implemented commitment cultures took the following steps:
- They invested in employee training. This is a way of demonstrating commitment to your employees’ growth. It also makes it clear that you want to retain your employees and their skills—you wouldn’t spend time and money training them if you wanted them to leave.
- They offered benefits such as flexible working and generous maternity leave packages. This shows that you care about your employees as people, rather than just as cogs in a machine.
- They were hesitant to lay off employees unless absolutely necessary, even during difficult times. This demonstrates that keeping your employees and providing them with security is more important than the quick-fix cash flow boost of redundancies.
Example: Transforming the Fremont Car Manufacturing Plant
In the mid-1980s, General Motors and Toyota partnered up to reopen a car plant in Fremont, California. They called their new venture the New United Motor Manufacturing, Inc., or NUMMI.
The Fremont plant had closed two years earlier due to a myriad of issues:
- Workers had taken no care in the work they did and had sometimes actively sabotaged the cars.
- Workers had drunk alcohol, taken drugs, and had sex while on the job.
- Productivity was low due to a prevailing attitude of “the production line never stops.” Even if workers spotted an issue with a car part, they couldn’t fix the problem until the car had reached the end of the production line. This often meant that the car had to be deconstructed to reach the faulty part and then reconstructed again—a time-consuming process.
Toyota planned to revolutionize the plant by introducing lean manufacturing. However, due to a union agreement, 80% of the reopened plant’s laid-off workers had to be re-employed. This meant Toyota had to introduce lean manufacturing to the misbehaving workers who’d become used to a completely different system.
Introducing Lean Manufacturing
As a first step, the Fremont plant’s employees were sent to a Toyota plant in Japan for two weeks to witness lean manufacturing in action. One such employee was Rick Madrid, who’d worked at the Fremont plant back in its pre-NUMMI days.
Building a Commitment Culture
While Madrid returned to Fremont full of optimism about lean manufacturing, not all of his colleagues were convinced. They were worried that their new-found power would come back to bite them. They feared retaliation if they made choices or suggestions that managers didn’t approve of. A culture of commitment hadn’t taken hold at NUMMI yet.
Because of the workers’ doubts, lean manufacturing wasn’t yet working in the factory. This became evident during a visit from NUMMI’s president, Tetsuro Toyoda. Toyoda noticed that a worker was having issues while installing a taillight. He asked the worker to pull the andon cord and stop the production line so that he could fix the problem. The worker was reluctant to pull the cord: he, along with many NUMMI workers, still feared negative consequences if he did so.
Eventually, Toyoda convinced the worker to pull the cord and fix the problem. Afterward, rather than chastising the worker for resisting pulling the cord, Toyoda apologized to him for not fully explaining to the plant managers the importance of encouraging workers to pull the cords. Toyoda also assured the worker that he was a crucial part of the plant’s success.
This incident finally convinced NUMMI’s workers that their managers did value them. It showed that NUMMI’s leaders were committed to helping every worker succeed, rather than blaming them when things went wrong.
From this point onwards, things changed at NUMMI. Workers began to pull the andon cords, and productivity increased. Within a few years, the Fremont plant was more productive than any other General Motors manufacturing site. Productivity levels had doubled compared to the plant’s pre-NUMMI days. Lean manufacturing and a commitment culture had transformed the plant and its workforce.
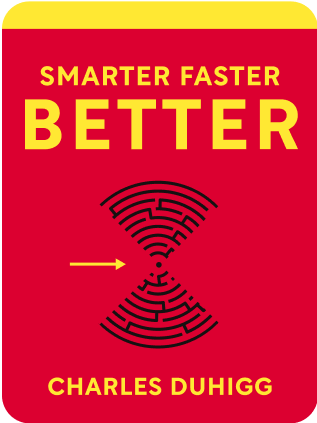
———End of Preview———
Like what you just read? Read the rest of the world's best book summary and analysis of Charles Duhigg's "Smarter Faster Better" at Shortform .
Here's what you'll find in our full Smarter Faster Better summary :
- Why becoming more productive isn’t about working longer hours or constantly pushing yourself to do more
- The 8 principles for improving productivity
- How to create a work culture in which each employee is truly valued