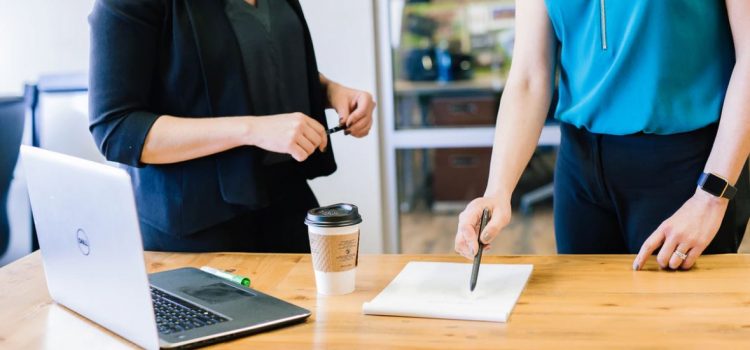
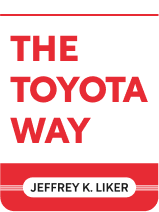
This article is an excerpt from the Shortform book guide to "The Toyota Way" by Jeffrey K. Liker. Shortform has the world's best summaries and analyses of books you should be reading.
Like this article? Sign up for a free trial here .
What is lean implementation? How can your business benefit from lean systems?
A lean system minimizes waste while also maximizing production within a company. Implementing lean manufacturing can also increase your workflow and create better teams.
Continue reading to learn more about lean implementation, as read in Jeffrey Liker’s The Toyota Way.
Practical Advice for Lean Implementation
To increase your chances of successful lean implementation in a business for the first time, Liker recommends the following:
- Tailor it carefully to your business. Replicating or benchmarking Toyota processes misses the point. As you problem-solve and improve, your version of lean will grow to fit your own business perfectly. It may not look anything like Toyota’s version.
- Start with a cleanup. A big cleanup (ideally using the 5S method) allows you to visually monitor the changes. However, the cleanup is only the beginning.
- Tackle heijunka early. Uneven production is the cause of many wastes. Evening out production is challenging, but doing this first will save time in the long term.
- Start small and be patient. Pilot lean ideas by creating a one-piece flow cell for a small part of the assembly line. Experiment with kaizen inside that cell using Plan-Do-Check-Act cycles.
- Maintain gains through close management. Toyota team leaders monitor their team daily to ensure efficiency gains don’t slide backward.
- Train your employees in problem-solving. If your workers don’t know how to solve problems when jidoka exposes them, production will go down rather than up.
- Make it a priority to coach new leaders. A key role of managers should be to train future managers.
Common Mistakes When Implementing Lean Systems
Liker also warns against common mistakes during lean implementation. When applying lean systems, don’t:
1. Make sudden, sweeping changes throughout the whole organization. This is the most common mistake people make when implementing lean systems, and it usually ends in disaster. Experiment in depth with a small one-piece flow cell first, then gradually extend these practices to other parts of the organization.
2. Focus too much on superficial changes. Lean production is about more than just mechanistic processes. Implementing it superficially or in a piecemeal fashion might lead to immediate gains, but these won’t be stable. Make sure your treatment of people changes alongside the physical processes.
3. Believe that lean will “fix” things. Lean processes are designed to “break” and reveal problems. Don’t be surprised if there seem to be more problems, not fewer, when lean systems are first introduced.
4. Get rid of middle management. Some organizations flatten their org chart when implementing lean systems. This is a mistake because it overburdens high-level leaders with direct reports, meaning that daily contact (which preserves efficiency gains and affords intensive coaching) is lost.
5. Declare it finished. Implementing lean systems is an ongoing activity throughout the life of the organization. As long as you’re still problem-solving and improving, you’re implementing lean systems.
Pay Attention to Leadership Involvement and Employee Morale
While the five common mistakes Liker cites stem from management overreach, some companies make the opposite mistake: too little top management involvement. According to Lean Factories, a manufacturing blog, top management sometimes takes a hands-off approach to implementing lean systems, which sends employees the message that lean programs aren’t that important. Further, when top leaders are disengaged, they can’t correctly assess funding requests for lean efforts.
Also, while Liker’s “mistakes to avoid” touch on employee morale, he doesn’t explore it in depth. If you’re planning to implement lean systems in your organization, Lean Factories recommends you also keep these morale-related tips in mind:
- Don’t implement lean systems for the sole purpose of cutting costs. Some companies create lean systems so they can spend less on overheard—in this case, the message you’re sending to your employees is that the more efficiently they work, the less job security they have. This can lead to low morale at best and sabotage at worst. Instead, use lean processes as a way to facilitate learning, growth, and expansion.
Don’t place the lean burden on one department. When employees on the shop floor are working hard to create products and there are a select few who tell them how to work faster, or better, this breeds resentment. Rather than having management impose lean systems on the factory workers, the systems should be applied to every department in the company.
Applying Lean Ideas Outside Manufacturing
While Liker gives some examples of businesses that have applied lean ideas outside the manufacturing sector, these are still broadly in the area of producing goods: software systems and assembling gift baskets. What about more complex work that doesn’t culminate in a tangible product?
An increasing number of hospitals are applying lean ideas to both administrative processes and patient care, with some proponents arguing that lean principles can save lives. The lean approach has also helped nonprofit organizations streamline their processes.
Some lean principles seem to work better than others in different sectors. For example, while Liker argues that the “just-in-time” principle can apply to information flows in knowledge work, there may be frustrating mismatches between the amount of information a manager wants to share and the amount of information an employee needs. The best solution may be to balance lean “just-in-time” learning with more traditional “just-in-case” learning.
In an office environment, you can apply lean principles to both the physical layout of the office and the knowledge work itself. In knowledge work contexts, employees can learn to:
- Eliminate waste
- Record, standardize, and improve the parts of their job that they repeat often
- Improve communication throughout the organization
- Solve problems quickly at their root
- Encourage a “coach” mentality in leaders.
However, note that if the knowledge work is primarily based on creativity and innovation, implement lean principles with caution—applying these principles too enthusiastically can eliminate as “waste” the unstructured time necessary to experiment with new ideas. As Liker advises, make changes gradually.
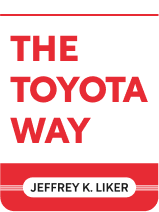
———End of Preview———
Like what you just read? Read the rest of the world's best book summary and analysis of Jeffrey K. Liker's "The Toyota Way" at Shortform .
Here's what you'll find in our full The Toyota Way summary :
- The story of how Toyota became the biggest automaker in the world
- An explanation of Toyota's lean manufacturing process
- Tips on how to apply Toyota's methods to your business