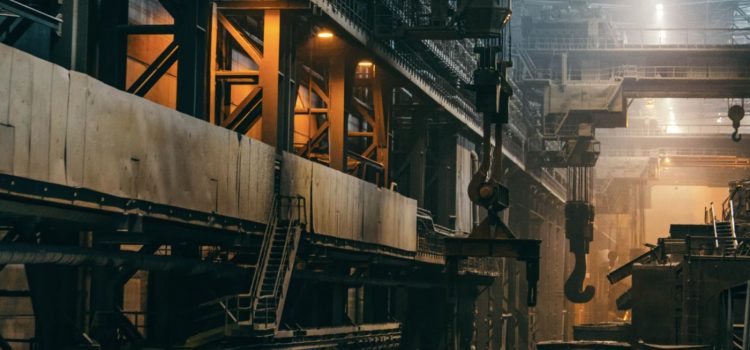
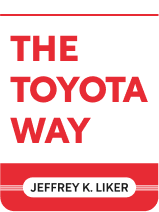
This article is an excerpt from the Shortform book guide to "The Toyota Way" by Jeffrey K. Liker. Shortform has the world's best summaries and analyses of books you should be reading.
Like this article? Sign up for a free trial here .
Where does Toyota’s cleanup process begin? What is the 5S implementation plan?
In The Toyota Way, Jeffrey Liker says that the heart of Toyota’s approach to efficiency is the concept of kaizen, or continuous improvement. To begin kaizen, you have to start with the 5S implementation plan to reduce waste.
Let’s go through the steps of the 5S implementation plan in detail.
What Is the 5S Implementation Plan?
The most common approach to starting kaizen is the 5S implementation plan:
- Seiri (sort): Get rid of unnecessary items.
- Seiton (systematize): Devise a logical system for storing and displaying the necessary items.
- Seiso (shine): Make sure everything stays in its place. Fix broken items.
- Seiketsu (standardize): Record rules and instructions and share them with everyone who uses the space.
- Shitsuke (sustain): Ensure that no parts of the system will deteriorate.
Liker comments that some lean consultants go into a business, do this cleanup, and declare kaizen complete. However, this is just the starting point.
(Shortform note: The effectiveness of 5S isn’t limited to manufacturing. People have also applied 5S in contexts ranging from hospital operating rooms, in which it minimized the number of potentially life-threatening interruptions during surgery, to engineering projects, in which 5S “audits” improved the transparency and efficiency of the process. With a twist, you can even apply it to your personal belongings. In Algorithms to Live By, Brian Christian and Tom Griffiths recommend that you position the items you use most frequently in the most accessible places.)
Jidoka (Intelligent Error Detection)
At Toyota, it’s crucial to expose defects early. Liker explains that in traditional manufacturing processes, large piles of inventory can hide defects that aren’t discovered until much later, making it hard to trace the cause of the problem. Toyota roots out defects by deliberately keeping inventory levels low and through jidoka (intelligent error detection). Jidoka prevents the wasted production of defective items during the 5S implementation plan.
Sakichi Toyoda’s loom—designed to stop automatically when it detected a single broken thread—is the prototypical example of jidoka. When the loom stopped, this was a signal that something was wrong and a call to fix the problem.
Applied to the assembly line, Liker calls this concept “in-station quality,” meaning that at each workstation, both people and machines inspect each newly received part and stop the line immediately if they detect a problem. Standard Toyota practices such as maintaining minimal inventory levels and a clear line of sight across the shop floor also help workers and supervisors to spot problems early. The signaling mechanisms that alert others that something is wrong are called andon. When an andon is activated, other team members come running to help solve the problem.
Liker points out that in terms of efficiency, this practice seems counterintuitive. How can an assembly line be efficient if it stops every time someone spots a defect? He argues that in the short term, stopping the assembly isn’t efficient. However, stopping the production line adds urgency to the problem-solving process, so problems are solved much faster than they would be if the line hadn’t been stopped. And in the long term, quickly detecting and solving errors dramatically improves the efficiency of the whole line.
(Shortform note: Fast error detection is also the message of the “1-10-100 Rule,” or the “Rule of Ten,” a heuristic that describes how the costs of errors multiply as the errors work their way through the manufacturing and supply chains. According to this rule, if it costs $1 to prevent a particular error, the cost of fixing the error later in the process will be $10. And if the error reaches the customer, it’ll cost the company $100.)
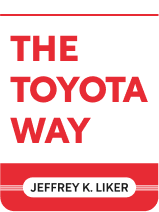
———End of Preview———
Like what you just read? Read the rest of the world's best book summary and analysis of Jeffrey K. Liker's "The Toyota Way" at Shortform .
Here's what you'll find in our full The Toyota Way summary :
- The story of how Toyota became the biggest automaker in the world
- An explanation of Toyota's lean manufacturing process
- Tips on how to apply Toyota's methods to your business